Nuclear Fuel Cycle
To prepare uranium for use in a nuclear reactor, it undergoes the steps of mining and milling, conversion, enrichment and fuel fabrication. These steps make up the front end of the nuclear fuel cycle.
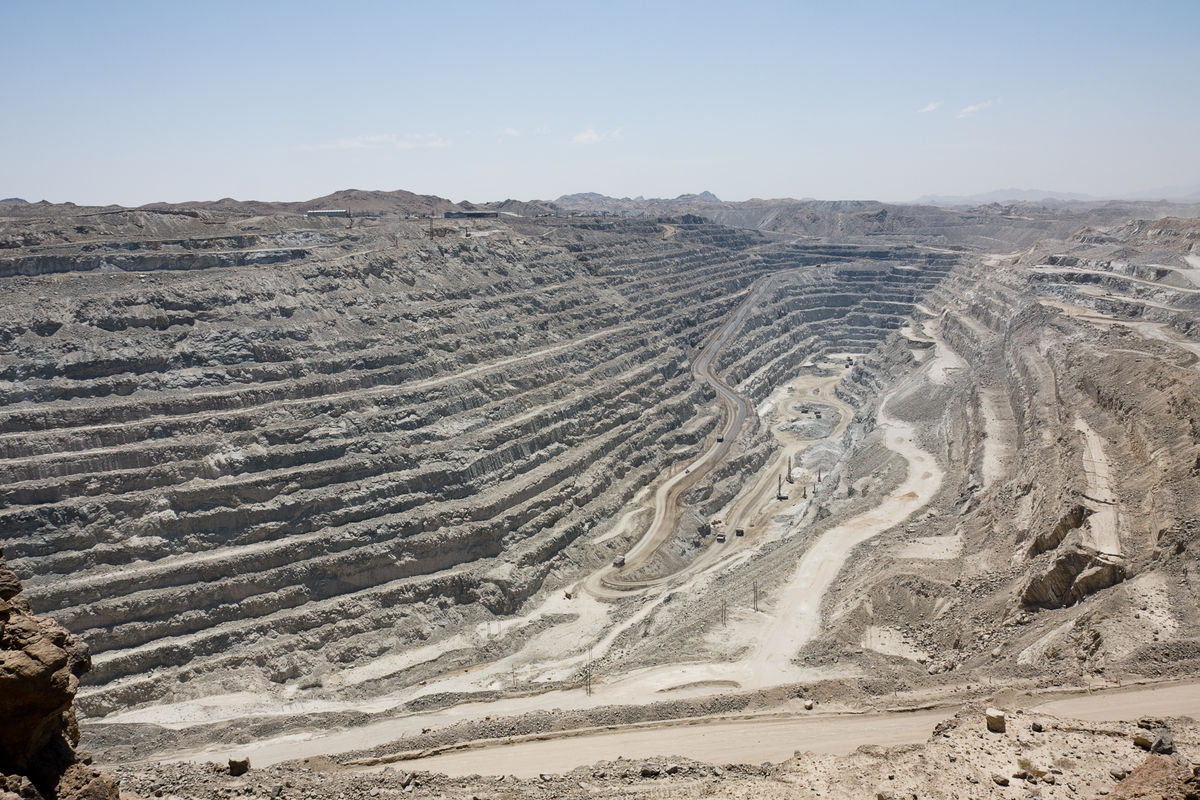
Uranium is mined by either surface (open cut) or underground mining techniques. The mined uranium ore is sent to a mill which is usually located close to the mine. At the mill the ore is crushed and is leached in sulfuric acid to allow the separation of uranium from the waste rock. It is then recovered from the solution and precipitated as uranium oxide concentrate (also known as "yellowcake").
Because uranium needs to be in the form of a gas before it can be enriched, the uranium oxide is converted into the gas uranium hexafluoride (UF6) at a conversion plant.
The vast majority of all nuclear power reactors in operation and under construction require enriched uranium fuel in which the content of the U235 isotope has been raised from the natural level of 0.7% to about 3.5% or slightly more.
Enriched UF6 is transported to a fuel fabrication plant where it is converted to uranium dioxide powder and pressed into small pellets. These pellets are inserted into thin tubes to form fuel rods. The rods are then sealed and assembled in clusters to form fuel elements, or assemblies, for use in the core of the nuclear reactor.
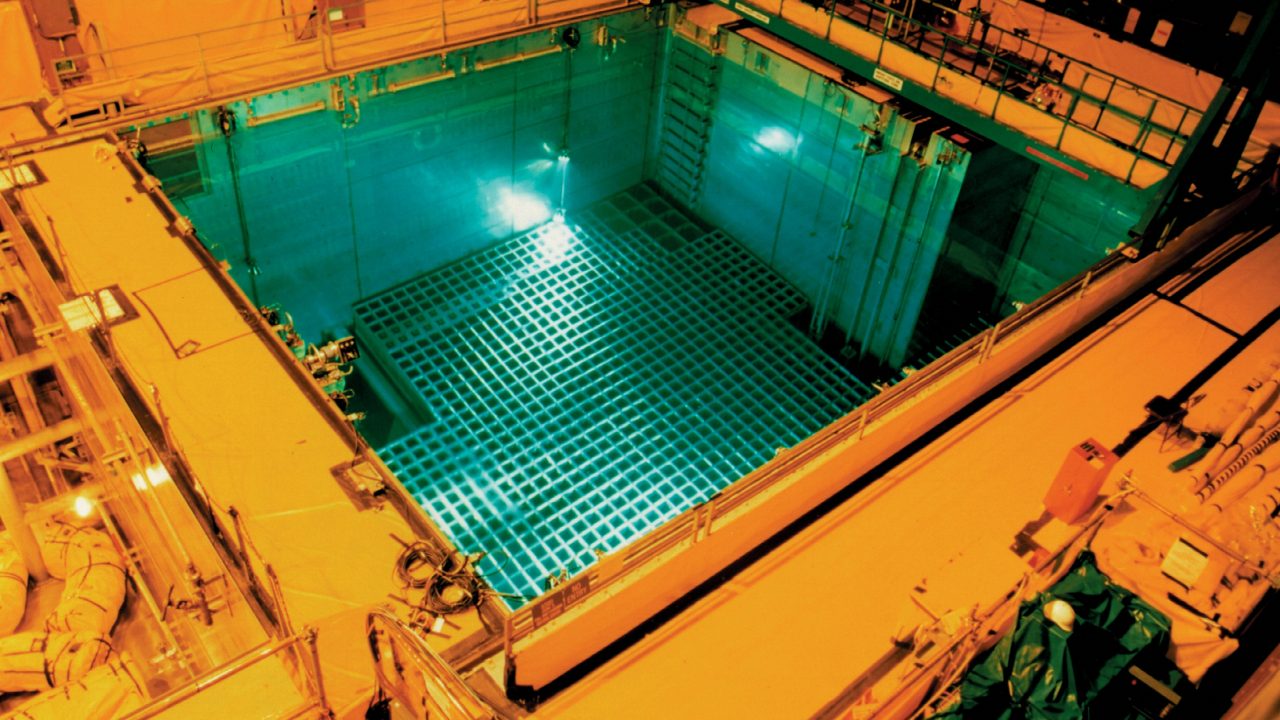
After uranium has been used in a reactor to produce electricity it is known as spent fuel and may undergo a further series of steps including temporary storage, reprocessing, and recycling before eventual disposal as waste. Collectively these steps are known as the back end of the fuel cycle.
To maintain efficient nuclear reactor performance, about one-third of the spent fuel is removed every year or so, to be replaced with fresh fuel.